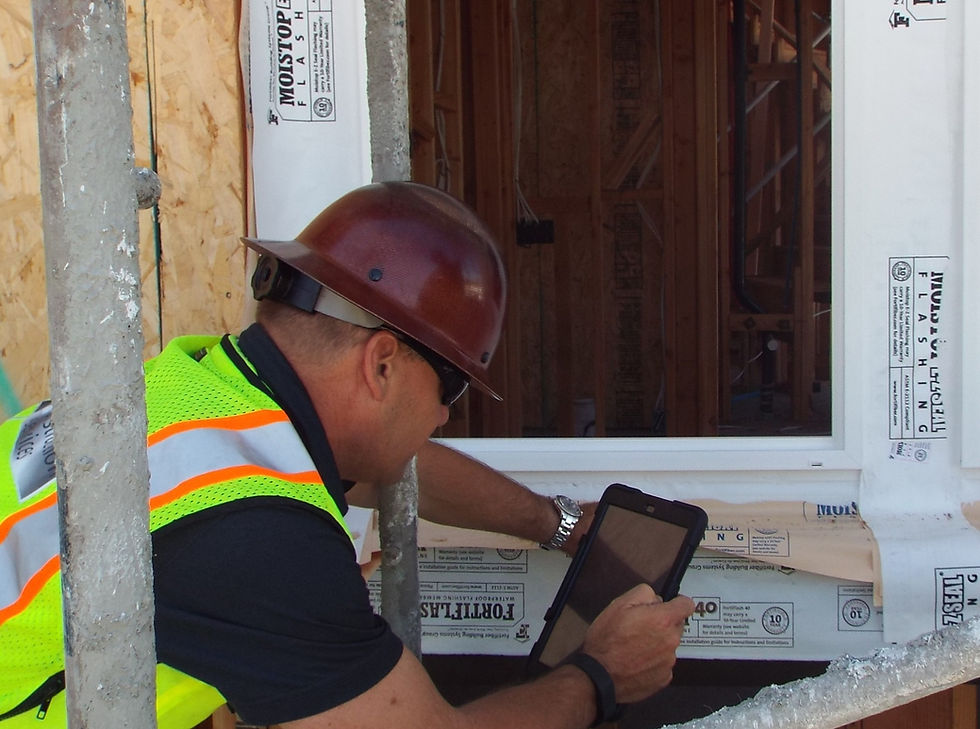
A quality assurance firm’s first-ever comprehensive report on building errors backs up general beliefs that home and commercial builders do far from shoddy work—but are nowhere near factory standards, either.
LJP Construction Services of Irvine, Calif., has made 42,000 inspections of about 1.1 million assemblies at 2,000 construction projects nationwide over the past four years. Over 40% of that work took place in California, where it found construction problems on 1.6% of its inspections of single-family homes. The company also provides inspection services (as well as architectural plan reviews and preventative maintenance manuals) on mid-rise and high-rise apartment, condominium, hotel and office towers across the US on hundreds of projects.
There’s less data on other states but far more reason for concern. Here are the deficiency rates in found for single- and multifamily structures in several states:

Some of the non-California numbers could be skewed because of the relatively small sample size in certain states. While LJP has done work as far away from home as Boston, it still is relatively new to the East Coast with over 100 active projects. LJP operates in 26 states, starting in California 25 years ago and in Florida since 2006.
LJP’s inspectors look for three kinds of deficiencies: Deviations from approved plans and specs, deviations from manufacturer recommendations, and problems with overall field quality. That last category includes sloppy installations as well as cases in which builders are employing decades-old products and technologies when newer, better ways to build abound.
“You can have a deficient assembly if you have selected an inferior product that can still perform but not as long as it should,” says Don Neff, LJP’s president. For instance, “Sisalkraft flashing is about as useful as a paper bag. That’s like using 50-year-old heart surgery tools. There are better products out there.” Installing such paper window flashing might still be OK officially, but to Neff, ”If you’re building to code, you’re just one step above breaking the law.”
Builders hire LJP in part because its quality assurance checks can protect the builder if they get sued, particularly in an age in which, according to Neff, some insurance carriers no longer are covering builders and others are raising rates and deductibles. Some insurers mandate that a builder hire a QA firm like LJP before even considering whether to write a policy, Neff says.
In most cases, the deficiencies that LJP spots aren’t so dire that the home will collapse, Neff says. But they could lead to warranty issues, such as when poor flashing of windows creates leaks or mold in new homes. LJP inspectors also have spotted cases in which recommended structural framing nailing patterns in shear walls weren’t followed in earthquake-prone areas.
LJP says the most significant deficiency types it sees in single-family homes nationwide involve exterior weather barriers, structural (wood) framing, mechanical, electrical and plumbing systems, and window/door installations, including preliminary weatherproofing assemblies. These findings jibe with a similar report from 2018 by Quality Built, another QA inspection firm.
Critics might regard California’s 1.6% single-family deficiency rate as woeful; imagine if your car had problems on 1.6 out of every 100 rides, or your smartphone hiccuped 1.6 out of every 100 times you used it. Neff, however, regards California’s performance today as proof that construction quality in the state has improved markedly. And this comes at a time when energy codes and other new regs are putting new demands on a home’s performance, he notes.
“Overall, California is doing very well with wood-framed structures, while other Sunbelt states need improvement, particularly with multi-family and townhome construction,” Neff said in a news release. “Weatherproofing assemblies are still the major problem but insulation and fire resistive assemblies are also poorly executed in the field. In our opinion, builders need to provide more training for their field supervisors and trade partners because the surveys show that many defects are likely from a lack of well-trained trade contractors.”
Comments